Производство и применение отечественных композиционных материалов в последнее время растет со среднегодовым темпом три – пять процентов. Таковы зарубежные оценки. Весьма сложные технологические процессы изготовления сырья, полуфабрикатов и собственно композитов не могут быть в одночасье заменены чисто российскими разработками, как, впрочем, и сама эта продукция весьма широкого ассортимента.
Длительное время и соответствующие технологии, и готовые продукты в этой сфере были в основном импортными – из Китая и ряда азиатских стран (до 60–65%), а также с Запада. Притом что советские композитные разработки, по имеющимся оценкам, используются минимум в 30 странах дальнего зарубежья, в том числе членами НАТО, включая Францию, Германию, Бельгию, США, Канаду.
Вряд ли нужно доказывать, сколь большое значение такие материалы имеют в оборонном комплексе, в продукции двойного назначения да и во многих гражданских отраслях. Потому у нас, как и на Западе, существует требование максимального самообеспечения по всем составляющим композитной отрасли, особенно в той ее части, что используется в ОПК.
Владимир Путин еще в 2008 году определил стратегическое направление, сказав, что Россия не должна зависеть от зарубежных поставок при выполнении оборонных заказов. Это касается и композитного сектора, тем более в связи со все более жестким санкционным режимом. Естественно, под эмбарго подпадают прежде всего продукция и технологии, которые могут использоваться в «оборонке».
В июле 2008-го правительство утвердило Федеральную целевую программу производства стратегических композитных материалов (углепластиков) для вооружения и военной техники, предусматривающую отказ от закупок более 300 видов комплектующих к 2020 году. В последующие пять лет принята «дорожная карта» по углеволокну, правительство утвердило план развития производства композитных материалов. В 2012–2016 годах была реализована российско-белорусская программа «Разработка инновационных технологий и техники для производства конкурентоспособных композиционных материалов, матриц и армирующих элементов».
По оценкам, звучавшим на международных форумах, состоявшихся в 2017 году, в реализации принятых решений сейчас задействовано свыше 60 предприятий и не меньше 30 профильных исследовательских центров. Импортозависимость в сегментах, связанных с производством и потреблением композитов, уменьшилась за последние 10 лет примерно на 15 процентов – до 30–35 процентов. Американские и британские источники оценивают ее примерно в 40 процентов, отмечая снижение за тот же период на 10–12 процентов. Но в сравнении со многими странами Запада, Китаем, Индией, Израилем, где композиты и их производные широко используются в судостроении, нефтегазодобыче и других материалоемких отраслях, востребованность углепластиков в России гораздо ниже. Это обусловлено длительной стагнацией в этом секторе отечественной экономики и как следствие пока еще низким спросом, к примеру, потребление композитов в судостроительном комплексе РФ пока не превышает одного процента от общемирового.
Так или иначе государство всерьез взялось за обеспечение ресурсной и стратегической безопасности композитной индустрии (КИ). Тренды в целом положительные, хотя по-прежнему сказывается пережитое в 90-е забвение проблем производственных отраслей страны.
Один из основных выводов форума по композитам, состоявшегося в конце октября 2017 года: среди главных причин, тормозящих активное импортозамещение, – низкая скорость внесения изменений в стандарты, относящиеся к новым материалам, неразвитость внутреннего рынка и недостаток кадров, разбирающихся в проблемах отрасли.
Характерно мнение Кирилла Комарова, директора блока по развитию и международному бизнесу госкорпорации «Росатом», высказанное на том же форуме: процесс сертификации нового композитного материала для оборудования занимает до трех лет, вдвое больше, чем за рубежом. Кроме того, необходим «более компактный порядок разработки стандартов, исследования и тестирования нужно проводить не последовательно, а синхронно». А чтобы применять новые материалы, недостаточно разрешить их фиксацию и описание в регламентах – нужны подготовленные кадры.
Согласно упомянутым программным документам к 2020 году объем производства композитных материалов и изделий из них должен составить 120 миллиардов рублей. Предусмотрены разработка и принятие не менее 550 нормативно-технических, нормативно-правовых и других документов, необходимых для развития отрасли. В конце октября 2017 года замминистра промышленности и торговли Сергей Цыб заявил, что для композитной сферы уже разработано и утверждено 363 новых стандарта, 25 сводов правил, 4 классификатора, 16 сметных нормативов и 5 профессиональных программ подготовки.
Нити заговора?
Наивысшие темпы роста показывает отечественное производство углеродного волокна (УВ). По данным директора по продажам Umatex Group Андрея Игнатьева, емкость отечественного рынка УВ – порядка 300 тонн с потенциалом кратного увеличения в ближайшей перспективе. В 2015-м введен в действие крупнейший в стране завод «Алабуга-волокно» годовой мощностью 1400 тонн УВ в год. К 2030 году это предприятие планирует войти в реестр крупнейших производителей УВ. Хотя завод уже сегодня производит в пять раз больше углеволокна, чем требуется российскому рынку, потому значительная часть продукции идет на экспорт. Однако есть опасения, что в связи с прогнозируемым ростом внутреннего спроса на УВ вывоз войдет в противоречие с внутренними потребностями.
Что касается термопластичных полимерных композиций, у России пока лишь двухпроцентная доля на мировом рынке, объем спроса в стране – не более шести миллионов тонн в год. Между тем импорт, по оценке эксперта «Полипластика» Сергея Киселева, в течение последних трех лет составляет минимум 25 процентов и может увеличиться в основном за счет того, что иностранные поставщики, особенно восточноазиатские, предлагают низко- и среднеценовой ассортимент, российские аналоги дороже, хотя в большинстве своем и более качественные.
Относительно смол для производства композитов есть нюансы. По итогам прошлого года потребление ненасыщенных полиэфирных смол составит не менее 45 тысяч тонн, причем около 80 процентов – российская продукция. Но в сегменте эпоксидных смол при емкости внутреннего рынка 40–42 тысячи тонн доля отечественных производителей не превышает 10 процентов. Данную нишу уверенно занимают зарубежные, в основном китайские поставщики. Их продукция опять же дешевле, зачастую за счет качества. Так что темпы импортозамещения в данном секторе обусловлены не только физическим ростом объемов производства, но и снижением себестоимости.
В сегменте химволокон-химнитей (ХВН), нетканых материалов и продуктов на их основе ситуация с импортозамещением остается сложной. Как отмечалось на прошлогоднем форуме «Выстраивание технологической цепочки выпуска синтетических материалов: от углеводородов до конечного продукта», необеспеченный внутренний спрос по этим изделиям остается не ниже 60 процентов, несмотря на рост российского производства в данном секторе. Среди причин дефицита – почти полная потеря в конце 80-х – 90-х годах мало- и среднетоннажной химии и ее сырьевой базы, а также близкая к стопроцентной зависимость большинства секторов химпрома от зарубежного оборудования. В товарном импорте преобладает все та же демпинговая продукция из КНР и развивающихся стран. Тем не менее за последние три года производство нетканых материалов с использованием ХВН в результате спроса в «оборонке» и других отраслях возросло на треть, что обеспечили прежде всего предприятия «Куйбышевазот», «Курскхимволокно», «Газпромхимволокно» и «Термопол».
Но крупнейший проект в означенном сегменте – полиэфирный комплекс в Ивановской области – до сих пор не реализуется, сроки начала строительства регулярно переносятся. Впрочем, это частная инициатива, не предусматривающая казенного финансирования. Эксперты отмечают, что негосударственный статус проекта сдерживает его осуществление, а это в свою очередь негативно сказывается на внутрироссийском производстве импортозамещающей продукции химпрома, в том числе и композитной.
На упомянутом форуме было предложено разработать комплексную «дорожную карту» развития отечественного производства ХВН и смежной продукции. И вскоре приказом Минпромторга была образована межведомственная рабочая группа во главе с замминистра Сергеем Цыбом по разработке плана мероприятий по развитию подотрасли искусственных и синтетических волокон и нитей на период до 2020 года. В составе – специалисты 20 профильных предприятий, включая, например, «Газпромхимволокно», «Союз производителей композитов», «Сибур», «Композит», НИИТЭхим, «Балаково Карбон Продакшн», «Химпроминжиниринг», «Казаньоргсинтез».
Или ПАН, или пропал
Перспективное развитие – это в первую очередь формирование межрегионального отраслевого промышленного кластера «Композиты без границ». Он создается с 2016 года по инициативе Umatex Group (входящей в Росатом). На конференции «Импортозамещение-2017» гендиректор компании Александр Тюнин, представляя проект, отметил, что ставится задача увеличить российский рынок углеродного волокна и материалов на его основе. Сейчас он составляет 0,5 процента от общемирового, а к 2025 году должен увеличиться вчетверо. В кластере будут созданы условия для крупных, средних и малых предприятий, а также для молодых бизнесменов, готовых организовывать передовые производства и разрабатывать новые высокотехнологичные продукты на основе композитов. 23 предприятия из Татарстана, Московской и Саратовской областей подтвердили заинтересованность в проекте. Ожидается, что кластер будет полностью сформирован до конца этого года.
Что же касается композитных и смежных НИОКР и проектов, необходимо выделить разработанную Пермским исследовательским технологическим университетом технологию использования вторичного углеволокна из полимерных композитов. Этими разработками руководит доцент Юлия Куликова. По ее словам, исследования по извлечению углеродных волокон из состава полимерных композиционных материалов (ПКМ) реагентными методами не имеют аналогов в России, они создают базу для формирования новой отрасли производства конструкционных и иных изделий. Главная цель проекта – увеличение жизненного цикла изделий из ПКМ, в том числе в авиационной и космической отраслях, в машиностроении, за счет повторного использования ресурсов. Достигнуто минимальное снижение механической прочности ПКМ из вторичного продукта в сравнении с материалами из первичных волокон. Внедрение такой технологии планируется на предприятиях по утилизации отходов «Уралпласт» и «Буматика». В Алабуге с помощью Фонда развития промышленности в этом году модернизируется печь для производства высококачественного стекловолокна. Стоимость проекта – около 900 миллионов рублей, из них 441,5 миллиона обеспечит льготный заем ФРП. По информации Минпромторга РФ, востребованность проекта обусловлена тем, что стекловолокно – среди наиболее конкурентоспособных армирующих материалов, используемых в основе композитных изделий. Оно же – основной продукт для производства материалов, разрешенных к применению в оборонной промышленности. Кстати, общемировое потребление стекловолокна составляет 85 процентов от объема всех применяемых волокон для армированных композитов и лишь 13,5 процента приходится на другие полимеры.
В начале 2017 года подписан договор о сотрудничестве между правительством Саратовской области и АО НПК «Химпроминжиниринг» о реализации проекта по производству углеродного волокна на площадке «Саратоворгсинтез». Это предприятие выпускает необходимое сырье – нитрил акриловой кислоты, из которого «Химпромнижиниринг» будет производить ПАН-прекурсор – белое волокно, составляющее основу композитных материалов. Проект обсуждался в администрации области еще в ноябре 2016-го. Тогда было заявлено, что инвестор вложит в производство 3,5 миллиарда рублей. Мощность завода в Саратове составит четыре тысячи тонн в год с последующим увеличением до 25 тысяч. Планируется реализовать данный проект в течение трех лет. На заводе в Балакове (Саратовская область) планируется производство готовой продукции на основе ПАН-прекурсора.
Автор: Чичкин Алексей
Первоисточник: https://vpk-news.ru/articles/40999
Цитирование статьи, картинки - фото скриншот - Rambler News Service.
Иллюстрация к статье - Яндекс. Картинки.
Есть вопросы. Напишите нам.
Общие правила поведения на сайте.
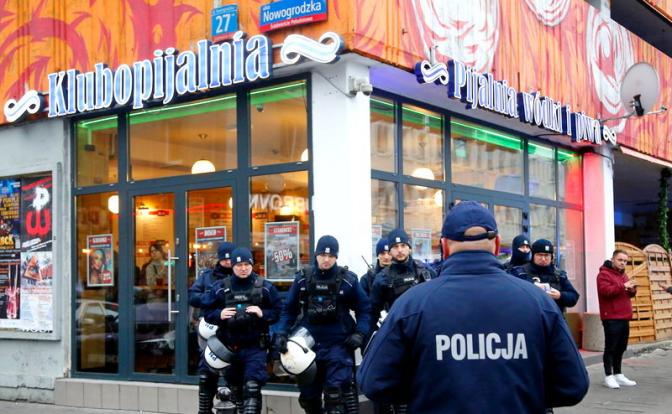
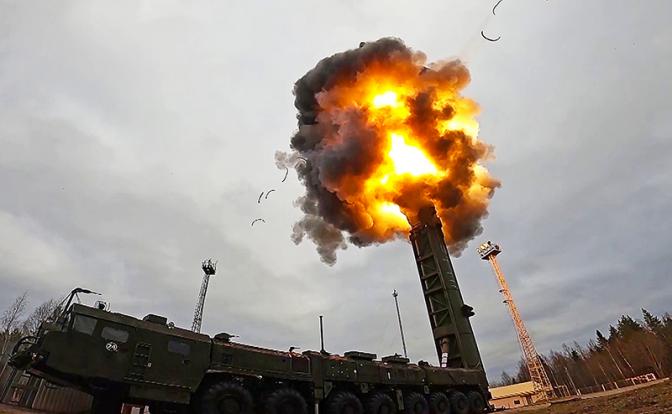
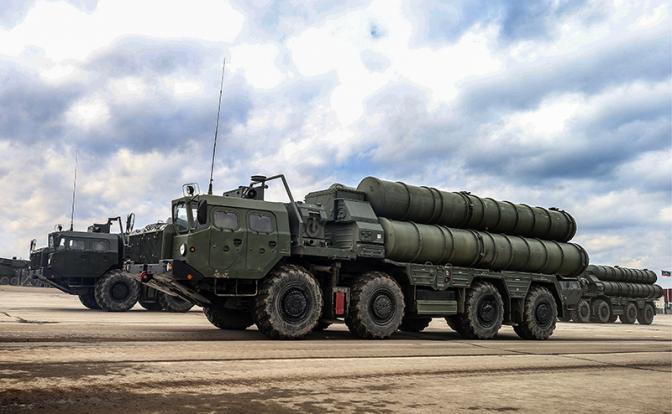
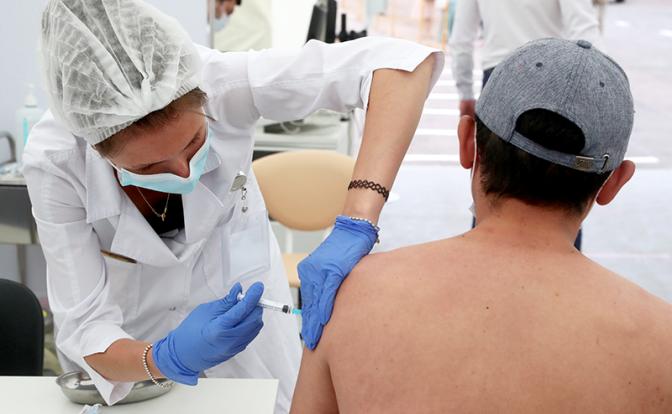
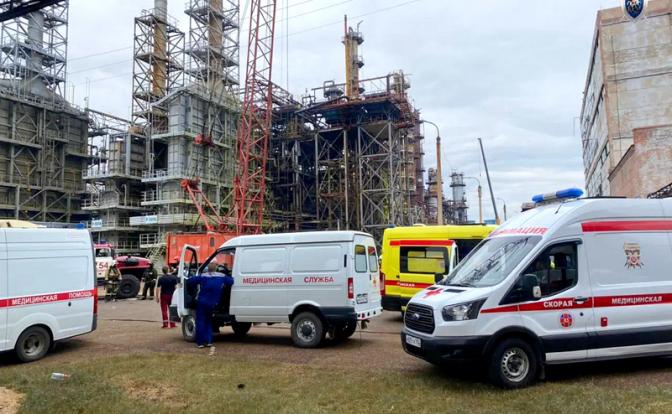